Scribe Marking
Scribe engraving process is an automated form of hand engraving. The diamond tip cuts through the material. The pressure is applied either via air powered cylinder head or an electrical solenoid. The pneumatically driven scribe head provides the pressure to assure the maximum possible depth of mark . The electrically driven marking pins make a lighter and shallower mark.
Two types of axes are available for the scribe engraving marking machines. A lead screw turns rotary motion into linear motion combining a screw and a nut where the screw thread is in direct contact with the nut thread. In comparison, a ball screw axis incorporates ball bearings into the screw mechanism. Recirculating balls within circuits, meaning that the screw shaft which passes through the ball nut rotates smoothly using ball point contact – which offers very low friction and close contact between ball and screw.
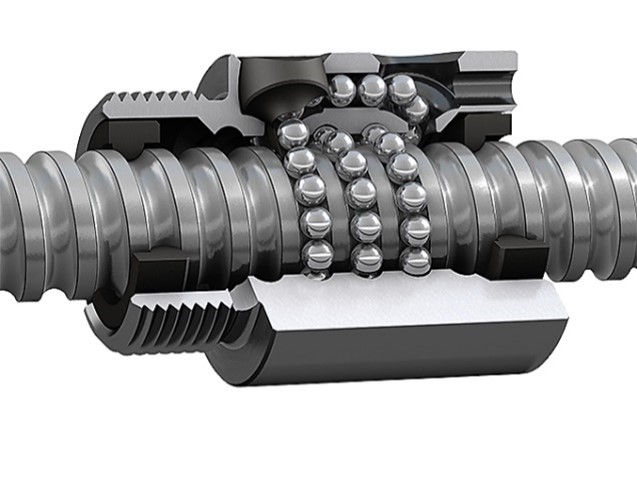
The ballscrew mechanism provides the best and most precise control over linear motion, with high efficiency and positional accuracy. Low friction means that you need less rotary input power to create the linear motion – allowing for a smaller powered motor; this also allows for a smaller footprint.
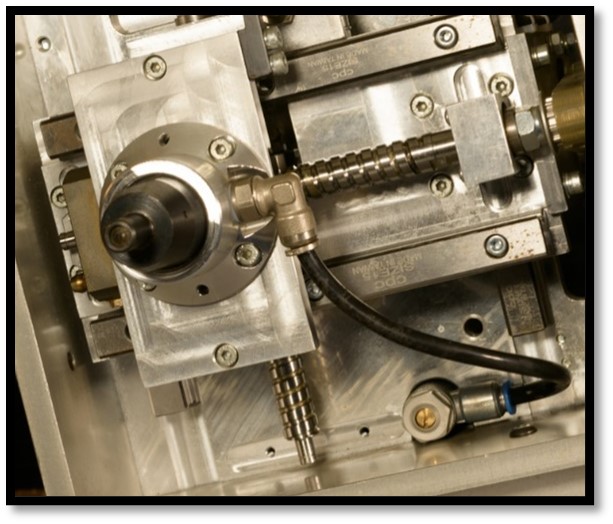
The most industrial machines use the ball screw drive in combination with multiple linear rails. Figure shows an example of a dual linear rail axis with the oversized ball screw drive. This marking machine is designed for heavy production and extended life. Scribe engraving machines are more than capable of meeting and exceeding many marking requirements in both durability and production speed.