Dot-Peen Marking
Definition Dot-Peen
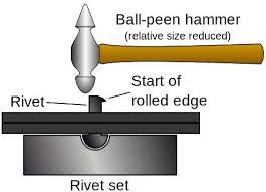
The name of the process Dot-Peen is derived from the word “Peen”. The peening process uses a hammer to change the shape metal. It is a cold forming process used to change the shape of rivets (Figure 1- Peen a rivet) and hold material in place, and many other uses.
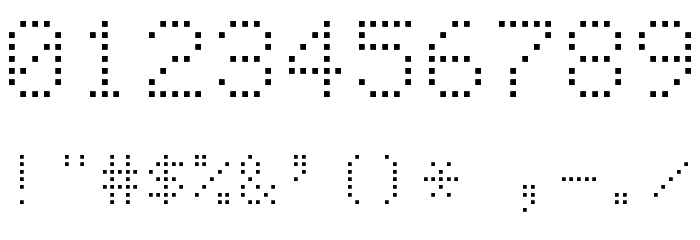
The “Dot” is used to describe the mark configuration. At the time of the invention of this marking process, Dot Matrix printers were the normal printing process. The characters in this printing process were made up of a series of dots as shown in Figure 2
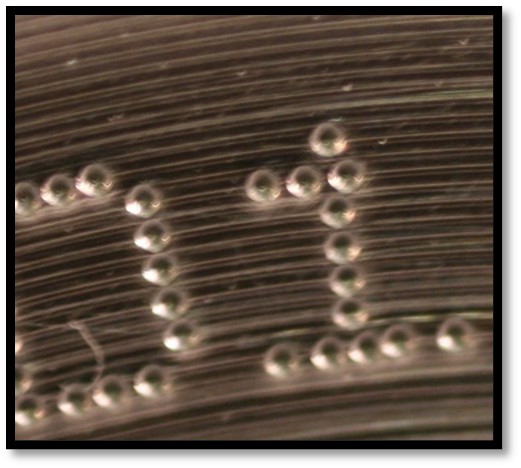
Figure 3 shows a close-up of a Dot-Peen mark. The marks are made up of a series of dots. These dots are depressed into the subsurface. The process is the combination of both peening and a series of dots.
Peen Definition
peen verb
\ ˈpēn \
peened; peening; peens
Definition of peen (Entry 1 of 2)
transitive verb: to draw, bend, or flatten by or as if by hammering with a peen
peen noun
Definition of peen (Entry 2 of 2) : a usually hemispherical or wedge-shaped end of the head of a hammer that is opposite the face and is used especially for bending, shaping, or cutting the material struck
Process
The Dot-Peen direct part marking process uses a fast-moving marking pin to peen (or stamp) a series of very small, closely spaced dots to form characters, designs, or machine-readable codes. The dots may be discrete or may blend into each other to form a more continuous line (Figure 4).
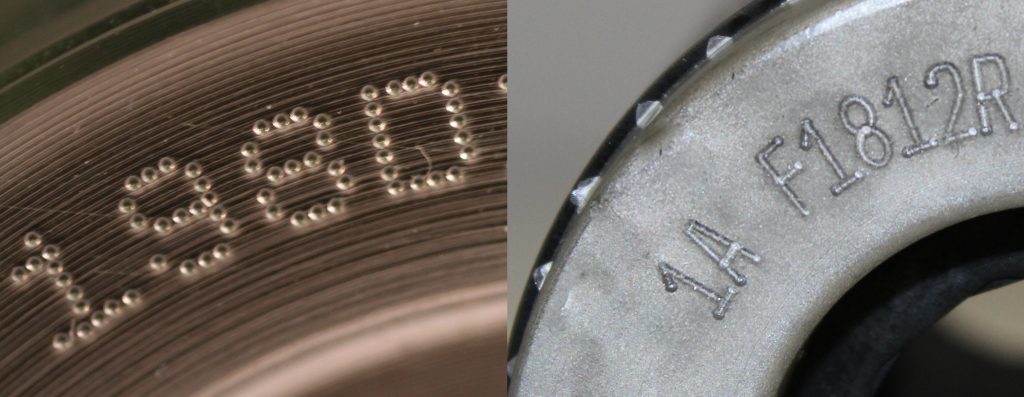
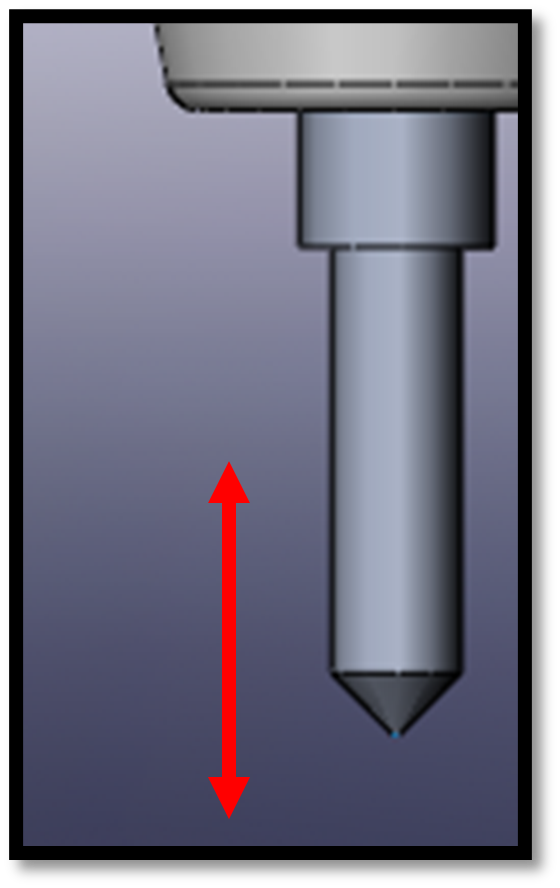
The small moving pin offers many advantages over indention (steel stamp) marking. The pin is small and exerts a limited force on the part substrate to indent just the dimple in the process to create the mark. The pin throw is amount of movement of the pin during the marking process. The pin throw is important to consider because the part must be placed within the pin throw to assure that the mark will be clear. The pin stroke is usually less than 12mm. The pin will indent the subsurface at any distance within the optimal pin throw, and therefore the Dot-Peen marking process can mark on slightly curved surfaces.
The pin assembly is mounted to at least 2 motorized axes. The stepper or servo motors move the marking pin assembly to form the characters and designs. Depending on the style and manufacturer of the marking machine the motors may move continuously or stop for discrete peens in the mark.